Green Refinery Challenges: Small-scale Sulfur Recovery
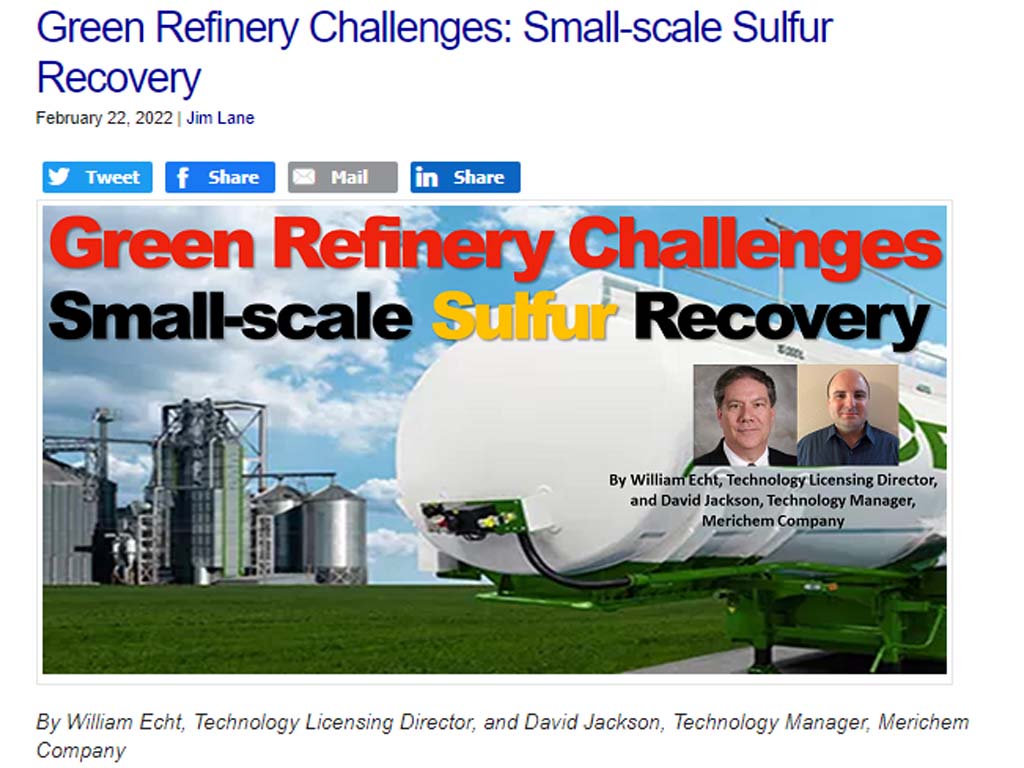
By William Echt, Technology Licensing Director, and David Jackson, Technology Manager, Merichem Company
Special to The Digest
Introduction
As part of the energy transition and refinery rationalization taking place around the world, many refiners are investigating projects for renewable fuels production (mainly diesel and jet fuel) from sustainable sources such as used cooking oils (UCO), waste animal fats (tallow) and/or certified sustainable vegetable oils, such as rapeseed. Some of these projects are being planned at existing refineries that will continue to process crude oil. Other projects are envisioned at idle refining facilities that have the infrastructure needed to accommodate new processing units.
One of the challenges for new processing technologies is the co-production of carbon dioxide (CO2) and maintaining active catalyst in the reaction system. A small amount of sulfur, usually in the form of liquid disulfide oils is added to the conversion reactors to maintain catalyst activity. This sulfur is converted to hydrogen sulfide (H2S) in the reactor system. An amine unit can remove the unwanted CO2 from the process, but also removes the H2S. The resulting acid gas stream contains far less sulfur than is practical to remove with a typical refinery sulfur recovery unit (SRU) using Claus technology.
A LO-CAT liquid redox process is serving as the SRU at one refinery in Europe. It is designed to remove about 4 metric tons per day of sulfur from an acid gas with up to about 7 mole% H2S. This paper discusses the design and operation of the new SRU after 18 months of operation.
HVO Process
Figure 1 is a simplfied diagram of a typical Hydrogenated Vegetable Oil (HVO) process. The waste feedstocks and vegetable oils are stripped of oxygen in first reactor. The catalyst used in this reaction often requires sulfiding to promote conversion chemistry and to avoid catalyst deactivation. Dimethyl-disulfude (DMDS) is typically used to sulfide the catalyst. The DMDS is converted to hydrogen sulfide (H2S) and the oxygen from the feedstock is converted to carbon dioxide (CO2) and water (H2O) during the deoxygenation reaction.
The resulting hydrocarbon liquids exit the reactor(s) and are routed to a three-phase separator where water is removed and vapors are collected for cleaning and recycling. The hydrocarbon liquids are routed to an isomerization reactor before being separated into various cuts to create light fuels, green jet fuel and green diesel.
The vapors from the separator are routed to an amine unit to remove the H2S and CO2 formed in the de-oxygenation reactor. The treated gas from the amine unit is rich in hydrogen and recycled to the HVO process, a slip stream may be used as fuel gas. Depending upon what other units may be operating at the refinery, additional acid gases may be processed in other amine units at site. This was true for the European refinery that is the subject of this paper. In particular, the large Claus units previously used had been idled
Figure 1 – Typical HVO Process Flow Schematic for Renewable Fuels
Sulfur Recovery Design Conditions
Table 1 shows the design conditions for sulfur recovery at the refinery. There are multiple sources of H2S. Some units could be offline while others are operating. Another design variable is that H2S concentration in the vapors leaving the HVO process is dependent upon the operating conditions over time. The age of the catalyst and the severity of temperatrure and pressure used in the deoxygenation reactor affect the amount of H2S produced. The result is a range of H2S concentrations and CO2 volumes exiting the downstream amine units. At the refinery under discussion, there are two amine unit acid gas streams and a sour water stripper overhead vapor stream being fed to the LO-CAT unit.
Table 1 – SRU Design Ranges
The specification for the treated gas in this refinery is “99.9% sulfur recovery” or 10 parts-per-million volume (ppmv) of H2S.
Sulfur Recovery Unit (SRU) Process Selection
The existing higher capacity Claus SRU had been shut down when oil processing ceased at this refinery. The typical minimum H2S content for a feed to a Claus unit is 35 mole%. That condition is not available when the HVO process is operating. Modified Claus units can operate with less H2S in the feed stream, but to achieve >99.9% sulfur recovery, a tail gas treating unit is required downstream of any Claus SRU, which increases cost. Turndown conditions can also negatively affect Claus unit sulfur recovery efficiency.
A highly flexible sulfur recovery process was needed to account for the range of feed gas conditions. The selected process also needed to be able to achieve high recovery percentages over a wide range of operating flow rates and H2S concentrations. Merichem’s LO-CAT liquid redox process has the features that were required by the refiner:
- No loss of sulfur removal efficiency at turndown conditions,
- No minimum H2S concentration in the feed acid gas stream,
- Multiple equipment system configurations available, and
- Fully guaranteed to meet customer requirements.
The LO-CAT Process
LO-CAT technology is a proprietary liquid reduction-oxidation (redox) process that converts H2S to solid elemental sulfur. The process utilizes an aqueous solution of iron, whose catalytic performance is enhanced by a proprietary blend of chemicals. The H2S is converted to elemental sulfur by redox chemistry according to the following overall reaction:
The Absorber reaction represents the oxidation of H2S to elemental sulfur and the accompanying reduction of the ferric (active) iron to the ferrous (inactive) state. The Oxidizer reaction represents the oxidation of the ferrous iron back to the ferric state.
LO-CAT technology produces a sulfur cake that is mostly solid sulfur but contains some moisture and proprietary chemicals. LO-CAT does not produce any other products or byproducts that require additional treating by the operator, including liquid waste streams. Because the reaction takes place in the aqueous phase at near-ambient temperatures, the process is inherently safe. The removal of sulfur is not affected by turndown conditions and the process can be applied to almost any vapor stream containing H2S.
Liquid redox is an economical process for H2S removal and sulfur recovery within a given range as shown in Figure 2. On the low end of sulfur recovery, non-regenerative chemical absorbents (scavengers) are likely to be more economical due to the low capital cost of a two-vessel design. As the sulfur removal requirement increases, operating costs become prohibitive using scavengers. This is when a liquid redox process is advantageous due to lower operating costs. The higher capital cost of a LO-CAT unit is quickly paid out in operating savings versus replacement of the non-regenerative scavenger.
On the high end of sulfur recovery, an amine unit + Claus SRU is likely advantaged. The reason is the higher operating cost due to excessive loss of LO-CAT chemicals when removing more than 20 tons/day of sulfur cake.
Figure 2 – Market Niche for Liquid Redox in Gas Processing
System Configuration
Merichem offers two basic configurations for the LO-CAT® process. Direct treatment of a sour gas stream uses a separate absorber and oxidizer. This configuration is a lot like an amine unit – a closed-loop circulating solution – but in lieu of steam for regeneration, the LO-CAT process uses air to oxidize the iron catalyst back to Fe+++, making it avaiable for reaction in the absorber.
When hydrocarbons are not present in the vapor stream (e.g. acid gas from an upstream acid gas removal unit or sour water stripper overhead vapors) Merichem often employs an autocircualtion unit that combines the absorber and oxidizer into a single vessel and eliminates pumping of the working solution. This flow scheme is shown in Figures 3. A sufur filter is used to take solid sulfur out of the working solution to produce a sulfur cake which can be used as fertilizer or sent to a landfill. Chemcials recovered during filtration are returned to the unit to reduce operating cost.
The system in Europe has been operating for 18 months. Its configuration utilizes a proprietary autocirculation vessel with a rectangular design. For simplicity, a cynlindrical autocirculation vessel is shown in Figure 3.
Figure 3 – Autocirculation LO-CAT Unit
In a cylindrical autocirculation unit the sour gas enters a centerwell absorber and flows co-currently downward with the liquid redox solution. Outside the centerwell, air is being sparged into the solution to oxidize the catalyst. This also lowers the bulk density of the solution, helping it rise within the oxidizer section. The rising solution outside the centerwell and the force downard inside the centerwell sets up circulation betrween absorber and oxidizer without the need for pumping. Over 45% of LO-CAT® systems use an autocirculation configuration.
Refinery Operating Results
The European refinery installed a rectangular autocirculation unit. This was enabled by the dilute concentration of H2S in the feed to the LO-CAT unit which began operation in August of 2019. The customer has been very satisfied with the performance of the unit.
In the summer of 2020 the liquid redox unit underwent its first turnaround. The LO-CAT® solution was drained and stored for further use after the unit was restarted. The autocirculation vessel was opened, cleaned and inspected. There was a small amount of sulfur buildup on the floor of the vessel. The unit was cleaned with a warm water wash and no corrosion was noted. The shutdown for maintenance took one week. That is the equivalent to 98% availability in the first year of operation.
Conclusions
The market for sustainable biofuels is growing. Projects installed in existing operating refineries that will continue to process crude oil can typically utilize existing Claus units to handle any increased demand for sulfur recovery. But in facilities without a working Claus unit or where the Claus unit is overloaded, bio- refiners are often unsure how to handle low-tonnage sulfur recovery.
The use of LO-CAT liquid redox technology allows Green Refineries to address low-tonnage sulfur recovery and achieve very low SO2 emissions. The reliable systems demonstrate high availability, low operating cost and consistently achieve sulfur removal guarantees.
Full Article Biofuels Digest