Green Refinery Challenges: Small-scale Sulfur Recovery
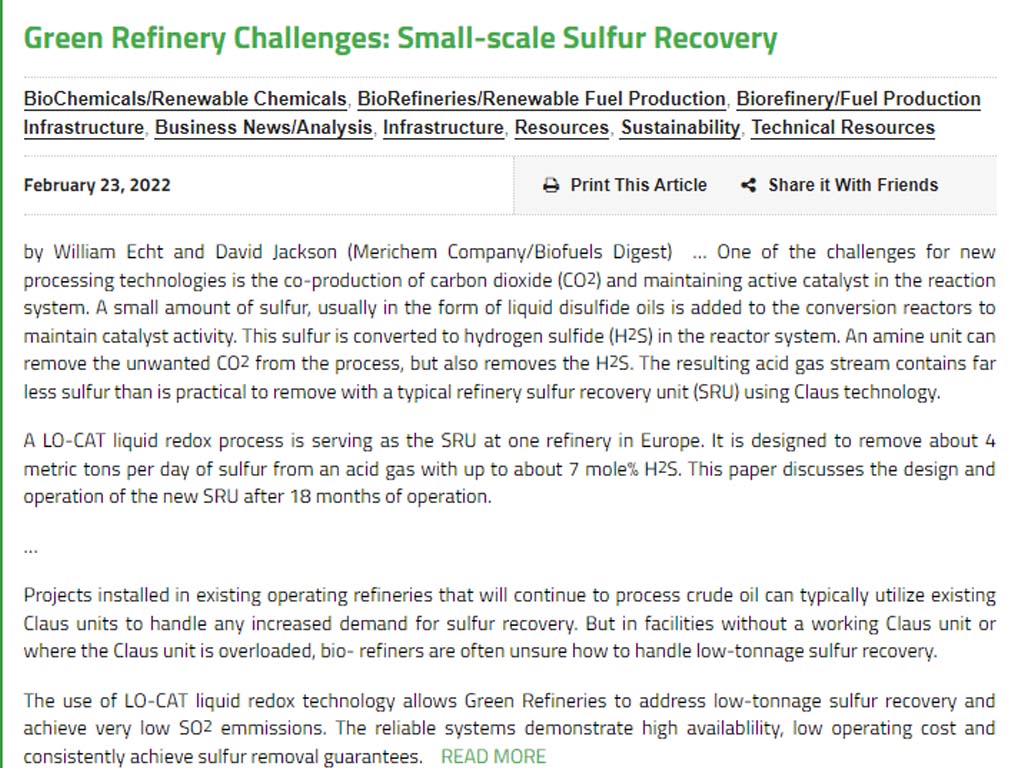
by William Echt and David Jackson (Merichem Company/Biofuels Digest) … One of the challenges for new processing technologies is the co-production of carbon dioxide (CO2) and maintaining active catalyst in the reaction system. A small amount of sulfur, usually in the form of liquid disulfide oils is added to the conversion reactors to maintain catalyst activity. This sulfur is converted to hydrogen sulfide (H2S) in the reactor system. An amine unit can remove the unwanted CO2 from the process, but also removes the H2S. The resulting acid gas stream contains far less sulfur than is practical to remove with a typical refinery sulfur recovery unit (SRU) using Claus technology.
A LO-CAT liquid redox process is serving as the SRU at one refinery in Europe. It is designed to remove about 4 metric tons per day of sulfur from an acid gas with up to about 7 mole% H2S. This paper discusses the design and operation of the new SRU after 18 months of operation.
…
Projects installed in existing operating refineries that will continue to process crude oil can typically utilize existing Claus units to handle any increased demand for sulfur recovery. But in facilities without a working Claus unit or where the Claus unit is overloaded, bio- refiners are often unsure how to handle low-tonnage sulfur recovery.
The use of LO-CAT liquid redox technology allows Green Refineries to address low-tonnage sulfur recovery and achieve very low SO2 emmissions. The reliable systems demonstrate high availablility, low operating cost and consistently achieve sulfur removal guarantees.
Full Article Advanced Biofuels USA